In the field trade industry, nothing will slow down a job more than poor planning. Missed deadlines, unorganised schedules, and last-minute changes can quickly turn a simple task into a mess. The good news is that it doesn’t have to be that way.
There is job scheduling software that can help you keep everything to assign tasks, manage timelines, and avoid unnecessary delays. A well-planned schedule will help to minimise the downtime of your field staff and do more jobs within a day. In this guide, we’ll show you how better planning and scheduling can keep your jobs running smoothly.
Why reducing job downtime matters
Every minute a job is delayed, your business loses money. It doesn’t matter whether you are waiting for materials, dealing with equipment breakdowns, or struggling with job scheduling; downtime slows down your operations.
The worst part of it is that most of it is avoidable. By understanding why downtime happens and how it impacts your business, you can take the right steps to keep things running smoothly and improve efficiency.
What is job downtime?
Job downtime refers to the periods when your operations stop or get delayed due to inefficiencies or unforeseen problems.
It can happen due to various reasons, such as equipment failure, supply chain issues, scheduling conflicts, or even miscommunication among teams. There are two main types of downtime. They are:
- Planned downtime: This includes scheduled breaks that you have pre-planned, such as routine maintenance, team meetings, or software updates. While planned downtime might seem like an interruption, it’s a good thing as it can help prevent bigger issues later by keeping everything in check.
- Unplanned downtime: These are the delays that arise from situations like equipment failures, last-minute cancellations, or miscommunication between teams. These delays can hurt your business the most and can bring your operations to a complete standstill.
How unplanned downtime affects profitability and efficiency
Let's be real; downtime isn't just annoying. It's expensive.
Every hour that you lose due to delays can hurt your business in many ways.
Let’s look at them briefly.
- Increased costs – Wasted labour hours, overtime pay, and last-minute adjustments can add up to your expenses.
- Missed deadlines – Delays can pile up your jobs and frustrate your clients, leading to lower retention rates.
- Lower productivity – When employees sit around waiting for the next step, efficiency takes a hit, making it harder to meet demand.
- Damaged reputation – Constant delays can hurt your brand image and drive customers to competitors.
What are the common causes of job downtime?
Downtime is usually caused by avoidable mistakes or poor planning.
Nevertheless, when the work stops, it is frustrating and costs you money. You need to have a clear idea about these causes so that you can have a better system in place to handle them. Here are some of the most common reasons field service businesses face downtime:
- Poor scheduling and planning: When you don’t plan the schedules properly, jobs can get delayed, technicians may idle without work, and the productivity of the whole business will drop. Further, if you come across overlapping appointments or last-minute changes, it can create chaos if you don’t have a good job scheduling software in place.
- Equipment breakdowns: If your tools or machines break down in the middle of a job, everything stops. They need to be maintained and serviced at the right time. Ignoring these routine maintenance only leads to bigger, costlier problems.
- Waiting on materials or parts: If you don’t have the necessary material in your hand and the supply chain is delayed, then it can bring a job to a halt. Ordering everything at the last-minute and depending on unreliable suppliers can make things worse.
- Miscommunication between teams: Poor and unclear communication between teams can lead to errors, confusion, and wasted time. It is difficult to satisfy your clients and avoid any delays if technicians, office staff, and customers aren’t on the same page. There should be better tools in place, like job scheduling programs to keep every related party connected in real-time.
- Customer delays or cancellations: Sometimes, the delay comes from the customer. If they forget an appointment, aren’t prepared, or cancel at the last minute, it can waste your valuable time. There is modern job scheduling software that will send automated reminders regarding upcoming jobs to every related party.
- Traffic and travel delays: Getting stuck in traffic wastes valuable work hours. If you have poor route planning systems, the technicians will spend too much time on the road instead of on the job. It can be difficult to tackle this challenge without job scheduling software that has GPS tracking and route optimisation features.
- Relying on manual processes: The use of paper schedules and handwritten job details will not cut out to the intense competition in today’s business world. These manual processes will slow you down.
- Lack of contingency planning: Unexpected problems like equipment failures, staff shortages, or supply delays can come up at any time. If you don’t have a backup plan, these issues can throw your whole schedule off.
How to minimise job downtime with better planning
It doesn't matter what kind of unplanned delay you face; every minute of downtime will cut into your revenue and profits.
The good news is, that you can prevent most of it with better planning. Let’s go through some simple, effective strategies that you can use to keep running your operations smoothly.
Plan with smart scheduling
A messy schedule is one of the biggest reasons for downtime. Further, overlapping jobs, last-minute changes, or not having the right people in place can also cause unnecessary delays.
Therefore, instead of reacting to problems as they come, you should use job scheduling software to plan. Look at past jobs, track busy seasons, and make sure every technician has enough time to complete their tasks without rushing to the other.
Use automation to keep jobs on track
Are you still keeping track of jobs manually? That’s asking for trouble because it’s easy to miss updates, lose paperwork, and face scheduling errors with a manual system. All of these will also waste your time and reduce your efficiency.
With modern job scheduling software, you can send updates automatically so that your team and clients get instant notifications. Therefore, you can handle last-minute changes without running into chaos. If a technician runs late or a job is cancelled, the system quickly assigns the next best job, reducing wasted time.
Prevent equipment breakdowns before they happen
Nothing stops a job faster than a tool breaking mid-task. That’s why you should do regular maintenance to avoid these situations instead of waiting till your equipment breaks. A simple and quick inspection before each job can help you detect small problems early and prevent costly downtime later.
Assign the right people for the right jobs
Not every technician is trained for every task. So, sending the wrong person to a job can lead to delays. If they don’t have the right skills or tools, they’ll have to reschedule or call for backup. You should use a modern job scheduling program that matches technicians to jobs based on their expertise.
Improve communication to avoid mistakes
Another one of the biggest reasons for downtime is due to shortcomings in communication. There should be a clear channel for a technician to communicate with the office, the clients, and vice-versa. Otherwise, technicians might show up at the wrong time, or a customer might not be ready to attend for a job.
Make sure to use real-time communication tools like mobile applications and job scheduling software with communication features to send instant updates and keep everyone informed. When your technicians know exactly what to do and customers know what to expect, delays will go down, helping you to complete jobs faster.
How scheduling tools help reduce downtime
As you can see, unplanned delays can affect the profitability of your business in many ways. However, you can use modern job scheduling tools to fix a lot of these problems. They help you organise jobs, manage last-minute changes, and keep your workflow smooth. Let’s dive in more and take a look at how this software can help you to avoid such delays.
Job scheduling software keeps things organised
Trying to manage jobs manually often leads to various errors such as double bookings and missed appointments etc. Job scheduling software takes care of this for you. It automates scheduling, assigns jobs based on availability, and sends reminders to both technicians and customers when the job is due.
When you can handle all these in one place, you don’t have to waste time on fixing scheduling errors and focus more on doing more jobs. Plus, automation will minimise errors, take away your stress, and you don’t have to scramble anymore, track your team, and monitor their progress.
Easily adjust schedules in real time
No matter how well you plan, things can change. A technician might call in sick, a job might take longer than expected, or a customer might reschedule. Without a proper system, these last-minute changes can cause chaos.
With job scheduling software, making such adjustments is easy. If a technician is running late, the system can reassign jobs on the go. If a job gets cancelled, you can quickly fill the gap with another one. This flexibility helps keep work moving, so no one is sitting around wasting time.
Make sure the right people and tools are available
A well-planned schedule doesn’t help much if your team doesn’t have the tools or materials they need. Job scheduling software helps you keep track of labour, equipment, and inventory so you don’t run into last-minute surprises.
For example, if a job requires a technician with a specific skill set, the system ensures the right person gets assigned. If a job needs special tools or materials, the software checks the availability of such tools and materials before scheduling.
Connect scheduling software with other business tools
Job scheduling software doesn’t just organise jobs. It can also work with other systems like invoicing, customer management, and inventory tracking systems in your business. Therefore, you don’t have to enter data into each system manually, which takes up more time and is prone to human errors.
For example, when a job is completed, the system can automatically send an invoice, saving time on paperwork. If new materials are needed, it can update the inventory and send a reorder request. When everything works together, you can run your business smoothly with less effort.
What are the best practices for effective planning and scheduling
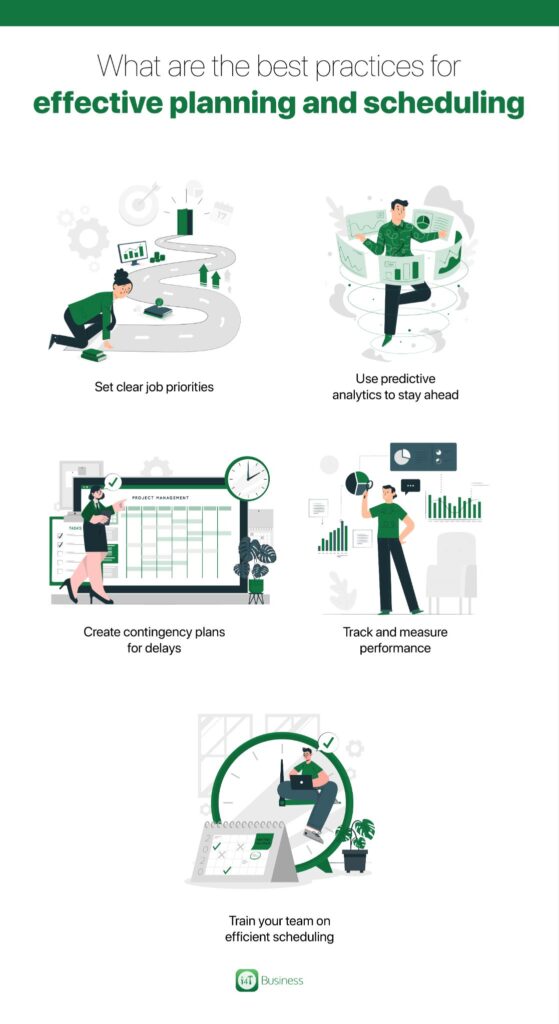
A good scheduling system is not just about assigning jobs to technicians. It’s also about prioritising tasks, preparing for setbacks, and continuously improving your workflow. Here are some best practices to help you get the most out of your planning and scheduling.
Set clear job priorities
Not all tasks are equal. Some jobs are time-sensitive, while others can wait. If your team isn’t sure which tasks to tackle first, you might risk losing important businesses that are time-sensitive.
Start by categorising jobs into critical and non-essential tasks. Urgent repairs, time-sensitive service calls, or high-value clients should be top priority. Routine maintenance or lower-impact jobs can be scheduled around them. When you set a clear priority system, your team can focus on what matters most.
Use predictive analytics to stay ahead
Unexpected delays can throw off your entire schedule. But what if you could anticipate issues before they happen? That’s where predictive analytics comes in.
By analysing past job data, weather conditions, customer demand, and technician performance, scheduling software can help you spot patterns. For example, if a particular service always takes longer in winter, you can adjust time estimates accordingly. This kind of data-driven scheduling prevents surprises and keeps your operations efficient.
Create contingency plans for delays
No matter how well you plan, things won’t always go smoothly. A technician might call in sick, a customer may cancel at the last minute, or equipment could fail. Without a backup plan, your team could end up idling.
Therefore, you should always have a contingency plan in place. For example, you could have an on-call staff for emergencies, build a buffer time into schedules, or have a process to reassign jobs quickly. A little preparedness can make the difference between a minor setback and a full-blown scheduling disaster.
Track and measure performance
If you’re not tracking your scheduling performance, you’re missing opportunities to improve. That’s why you should track how long jobs take. Are technicians arriving on time? Where are the biggest bottlenecks?
Analytics in modern job scheduling software and performance reports helps you identify problem areas and make smarter decisions. If a specific type of job is always running late, you can adjust your scheduling approach. The more you track, the easier it is to fine-tune your process and cut down on delays.
Train your team on efficient scheduling
A great scheduling system only works if your team knows how to use it. If technicians don’t understand priorities, struggle with scheduling tools, or fail to update job statuses, it can lead to delays.
Regular training ensures that everyone follows the same scheduling process. Therefore, you must teach your team how to manage their time effectively, update job progress in real time, and handle unexpected changes.
Common scheduling challenges and how to overcome them
No matter how much effort you put into planning, scheduling jobs isn’t always easy. However, you can tackle these challenges with the right approach. Let’s look at some common issues and how to solve them.
Resistance to change: getting your team on board
Switching from manual scheduling to a digital tool can feel overwhelming for some employees. Technicians who are used to old-school methods might hesitate to adopt new scheduling software, thinking it’s too complicated or unnecessary.
When trying to fix this situation, you should show them the benefits of the software. Explain how job scheduling software makes their lives easier by minimising scheduling mix-ups and paperwork and its ability to give real-time job updates.
Offer them hands-on training and start with simple features before rolling out advanced options. When employees see how scheduling tools save them time, they’ll be more open to using them.
Inconsistent scheduling methods: creating a standard process
If different team members schedule jobs in different ways, things can get messy fast. One technician might schedule appointments in a notebook, another in a spreadsheet, and someone else might just rely on memory. All of these old-school methods will lead to scheduling errors like double bookings and missing appointments, etc.
The solution to this is to create a clear, standardised scheduling process for your entire team. You can use a centralised job scheduling system where everyone logs job details in the same place. When everyone uses this system, you can easily avoid any confusion and scheduling conflicts and do your operations smoothly.
Managing last-minute changes: staying flexible without chaos
Last-minute changes like customers rescheduling, jobs taking longer than expected, and technicians calling in sick are unavoidable. However, they don’t have to derail your entire schedule.
The best way to handle this is with a flexible scheduling system. Use job scheduling software that lets you reassign jobs in real time, shift appointments around easily, and notify technicians and clients instantly about any changes to their jobs. Having backup staff or buffer time built into your schedule also helps ensure that a small change doesn’t create a big disruption.
Balancing cost vs. efficiency: finding the right approach
Sometimes, optimising schedules for maximum efficiency can come at a cost. Hiring extra staff, investing in job scheduling software, or adding buffer time to prevent delays might seem expensive at first. On the flip side, cutting costs too much can overwork your team, rush them into jobs, and you might even face more scheduling conflicts.
The key solution here is to find the right balance. Look at your job history, track performance data, and invest in tools that genuinely help your business run better. A well-structured, efficient schedule saves money in the long run by reducing time wastages and downtime and improving customer satisfaction.
Wrapping it up
Downtime is frustrating, costs you money, delays the projects, and negatively impacts customer satisfaction. But as you can see, most downtime is preventable with the right planning and scheduling strategies.
Old school methods where you used pen and paper and spreadsheets are long gone. Modern job scheduling software has taken that place by automating job scheduling, tracking job progress in real-time, and helping you adapt to unexpected changes
With the right tools, you can reduce scheduling errors, improve communication with the team and clients and optimise resource allocation to run your business efficiently.
If downtime has been slowing your business down, now is the time to take control. Are you tired of missed appointments, last-minute scheduling chaos, and downtime? i4T Business has modern features that make job scheduling easy, help you plan, and manage changes in real time, and keep your team productive.
With our job scheduling software, you can easily stay organised, reduce delays, and complete more jobs with less hassle. Don’t just take our word for it. Try the i4T Business trial version for free today and see how our software can help you stay on top of your operations.
FAQs
Unplanned absences can create scheduling gaps. Use job scheduling tools to monitor technician availability and quickly adjust assignments when needed.
.
Slow seasons lead to idle staff, while during peak seasons, staff will overwork. Analyse these trends and adjust staffing levels accordingly to optimise your scheduling year-round.
If the customers are not ready for a job, they might refuse to receive your technician. Send reminders, confirm appointments, and ensure they have everything prepared before the technician arrives.
Your technicians might spend too much time on the road due to poor route planning. Use modern job scheduling software like i4T Business with GPS tools to optimise routes and minimise travel delays.
Unforeseen delays can happen. Adding a buffer time between jobs can help prevent small delays from affecting the entire day’s schedule
Hot off the press!
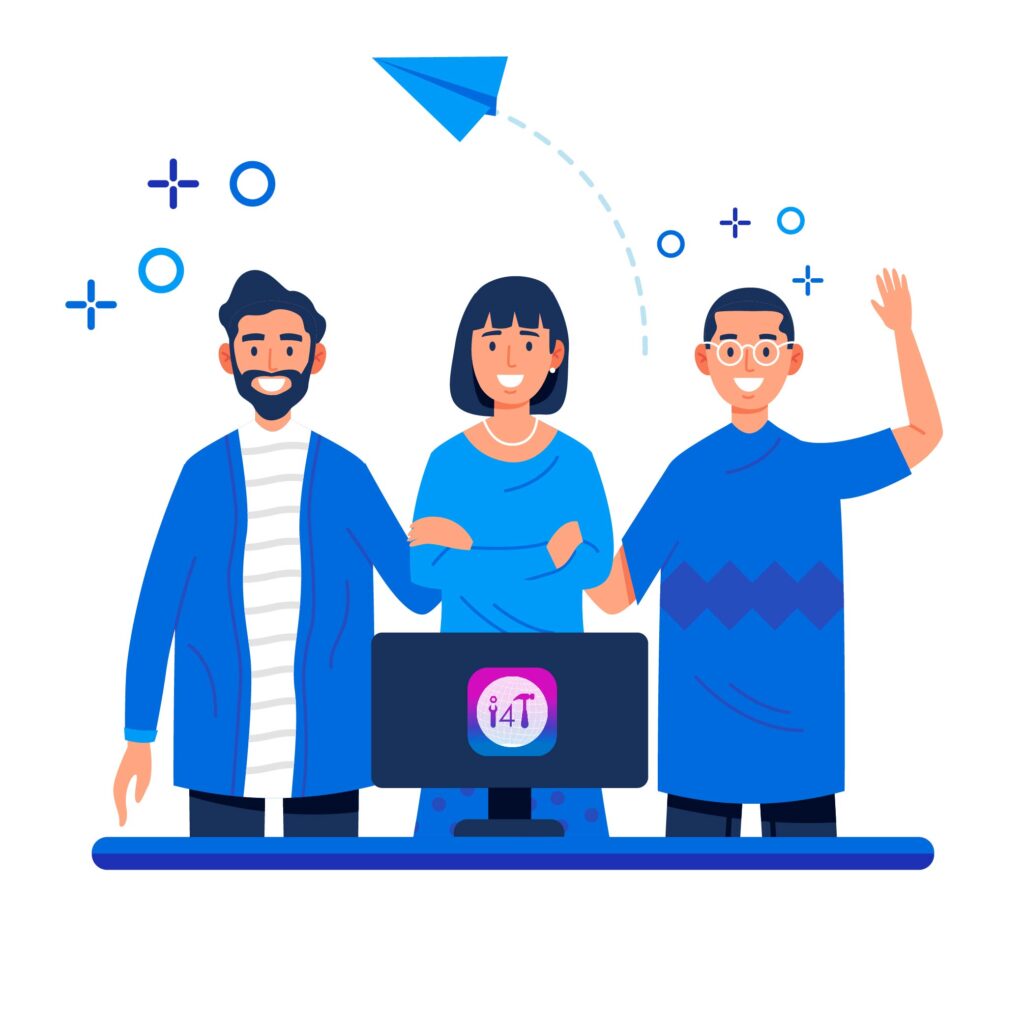
Field Service Management sector operates, the i4TGlobal Team loves to share industry insights to help streamline your business processes and generate new leads. We are driven by innovation and are passionate about delivering solutions that are transparent, compliant, efficient and safe for all stakeholders and across all touch points.